Food safety management software serves as a digital command center for maintaining rigorous food safety standards across operations. This specialized technology automates and streamlines critical processes, from temperature monitoring to compliance documentation, ensuring consistent adherence to food safety protocols.
The stakes in food safety management remain exceptionally high. A single safety breach can lead to:
- Severe health consequences for consumers
- Devastating financial losses
- Permanent damage to brand reputation
- Legal ramifications and regulatory penalties
Modern food businesses face complex challenges in maintaining safety standards:
Supply Chain Complexity: Managing multiple suppliers, tracking ingredients, and ensuring compliance at every touchpoint
Regulatory Requirements: Navigating evolving food safety regulations across different jurisdictions
Documentation Demands: Maintaining accurate, accessible records for audits and inspections
Food safety management system software addresses these challenges through:
- Real-time monitoring and alerts
- Automated documentation and record-keeping
- Centralized data management
- Integrated compliance tools
- Supply chain visibility
The right software solution transforms food safety from a demanding obligation into a streamlined, proactive process that protects both consumers and businesses. This digital transformation eliminates manual errors, reduces operational costs, and provides peace of mind through comprehensive safety oversight.
Key Features to Look for in Food Safety Management Software
Selecting the right food safety management software requires careful consideration of essential features that drive operational excellence. A robust solution should incorporate comprehensive functionalities designed to safeguard food safety standards while optimising business processes.
Critical Features for Effective Food Safety Management:
- Real-time Monitoring Systems: Temperature tracking across storage units, immediate alerts for compliance breaches, live data collection and analysis
- Digital Documentation Management: Centralised storage of safety protocols, automated record-keeping, version control for procedures
- Quality Control Tools: Customisable inspection checklists, non-conformance tracking, corrective action management
The integration of these features creates a unified system that strengthens food safety governance while reducing operational complexities. Advanced software solutions transform traditional manual processes into streamlined digital workflows, minimising human error and ensuring consistent compliance.
Risk Reduction Through Automation:
- Standardised processes across multiple locations
- Reduced paperwork and administrative burden
- Enhanced accuracy in data collection
- Quick access to critical safety information
- Improved response time to potential hazards
These technological capabilities establish a foundation for maintaining the highest food safety standards while optimising resource allocation and operational efficiency.
1. HACCP Planning and Management
HACCP (Hazard Analysis and Critical Control Points) is the foundation of effective food safety management. Food safety management software takes traditional HACCP protocols and turns them into flexible digital systems that can identify, monitor, and control potential hazards throughout the food production process.
Systematic Tracking of Hazards
Advanced software solutions offer a systematic way to track various types of hazards:
- Biological hazards: Bacteria, viruses, parasites
- Chemical hazards: Cleaning agents, pesticides, allergens
- Physical hazards: Glass, metal, plastic contamination
Automated Monitoring of Critical Control Points
The digital HACCP management system automates the monitoring of critical control points through:
- Real-time temperature logging
- pH level tracking
- Time-temperature documentation
- Corrective action protocols
- Alert notifications for threshold breaches
These automated systems replace manual record-keeping with accurate digital documentation, minimising human error and ensuring consistent monitoring of critical control points. The software keeps detailed records of each monitoring activity, creating a continuous chain of documentation for compliance verification and audit purposes.
Customisation for Specific Production Processes
Modern HACCP software allows for customisation of control points and parameters to align with specific production processes. This ensures that hazard prevention strategies are tailored to different food handling operations.
2. Compliance Management
Food safety management software must address the complex web of regulatory requirements across different jurisdictions. The right software solution helps businesses navigate:
Global Standards Compliance
- ISO 22000 certification requirements
- BRCGS food safety standards
- FDA regulations
- FSMA compliance protocols
Regional Requirements
- Local health department regulations
- Country-specific food safety laws
- Industry-specific standards
Effective compliance management features include:
- Real-time regulatory updates
- Automated compliance checks
- Digital documentation storage
- Customisable compliance checklists
- Alert systems for expiring certifications
- Audit-ready reporting capabilities
These tools create a systematic approach to maintaining compliance documentation, reducing manual errors and streamlining verification processes. Advanced software solutions integrate regulatory changes automatically, ensuring businesses stay current with evolving food safety standards while maintaining detailed records of compliance activities.
The digital documentation system enables quick access to required certificates, permits, and inspection reports, creating an organised repository of compliance-related materials essential for audits and regulatory inspections.
3. Traceability and Reporting
Effective food safety management software provides comprehensive supply chain visibility from farm to table. Advanced traceability features enable businesses to:
- Track raw materials through receipt, processing, and distribution
- Monitor product location and status in real-time
- Document temperature controls during transport
- Record batch numbers and expiration dates
- Identify product origins and destinations instantly
The automated reporting capabilities transform data collection into actionable insights:
- Customisable Reports: Generate detailed reports on demand for different stakeholders
- Digital Documentation: Store and retrieve critical records within seconds
- Real-time Alerts: Receive immediate notifications for any compliance breaches
- Inspection Ready: Maintain organised documentation for surprise audits
These robust traceability and reporting features enable rapid response to food safety incidents. Businesses can quickly:
- Isolate affected products
- Execute targeted recalls
- Identify root causes
- Implement corrective actions
- Document incident resolution steps
The integration of IoT sensors and mobile devices enhances data accuracy while reducing manual entry errors, creating a reliable chain of custody throughout the food supply network.
4. Risk Assessment and Predictive Analytics
Advanced food safety management software uses AI-driven analytics to turn raw data into useful information. These complex systems look at past trends, current data, and environmental factors to find potential risks before they become serious problems.
Key risk prediction capabilities include:
- Temperature fluctuation patterns
- Equipment performance metrics
- Ingredient quality trends
- Staff behaviour analysis
- Supply chain disruption indicators
The software’s predictive algorithms create risk scores based on multiple data points, triggering automated alerts when specific limits are exceeded. This proactive approach enables food businesses to:
- Detect equipment failures before they happen
- Identify high-risk ingredients or suppliers
- Spot potential contamination risks
- Predict maintenance needs
- Optimise storage conditions
Through continuous trend analysis, the system learns from past incidents and adapts its predictive models, becoming increasingly accurate at forecasting potential hazards. This data-driven approach shifts food safety management from reactive to proactive, reducing the likelihood of expensive incidents and protecting both consumers and brand reputation.
5. Automated Workflows
Food safety management software transforms manual processes into streamlined digital operations through automated workflows. These systems eliminate tedious paperwork by digitising:
- Daily temperature checks
- Hygiene inspections
- Inventory monitoring
- Expiry date tracking
- Cleaning schedule management
The automation of routine tasks reduces human error and ensures consistent regulatory compliance. Digital checklists prompt staff to complete required checks at scheduled intervals, while automated alerts flag potential issues before they escalate into serious problems.
Advanced workflow automation features include:
- Smart Scheduling: Automatic task assignment based on staff roles and schedules
- Real-time Notifications: Instant alerts for missed checks or compliance breaches
- Digital Sign-offs: Electronic verification of completed tasks
- Automated Reports: Generation of compliance documentation on demand
These automated processes create an auditable trail of food safety activities, saving valuable staff time while maintaining rigorous standards. The reduction in manual data entry allows teams to focus on critical food safety tasks rather than administrative duties.
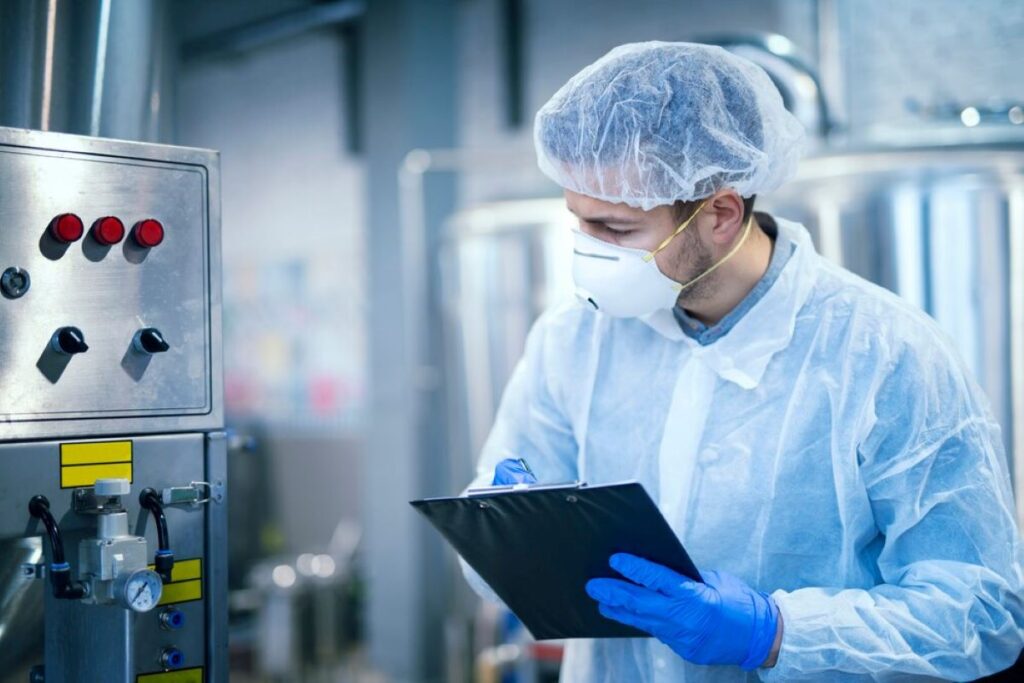
6. Supplier Management
Effective supplier management is a crucial part of food safety management software. These features provide a centralised system for keeping track of supplier credentials, certifications, and performance records.
Key Documentation Management Features:
- Digital storage of supplier certifications
- Automated expiry notifications
- Real-time updates on compliance status
- Secure document sharing portals
The software allows for systematic supplier auditing through:
- Customisable audit checklists
- Risk-based assessment tools
- Non-compliance tracking
- Corrective action monitoring
Advanced systems include supplier scorecards to assess performance metrics such as:
- On-time delivery rates
- Quality compliance scores
- Food safety incident records
- Response times to quality issues
These tools enhance supply chain integrity by establishing clear communication channels between organisations and suppliers. Digital platforms simplify the sharing of critical information, from updated certifications to audit findings, creating a seamless flow of documentation that supports food safety compliance.
The integration of supplier management features with broader food safety protocols assists businesses in maintaining consistent quality standards throughout their entire supply network while minimising the administrative burden of manual tracking systems.
7. Training Management
Staff training is essential for maintaining high food safety standards. Advanced food safety management software replaces traditional training methods with interactive, trackable learning experiences.
Key Training Management Features:
- Digital learning modules customised to specific roles
- Real-time progress tracking and completion certificates
- Automated scheduling of refresher courses
- Multi-language support for diverse workforces
- Interactive assessments and knowledge checks
The software creates a systematic approach to education through:
- Standardised Training Protocols
- Step-by-step guides for contamination prevention
- Visual demonstrations of safety procedures
- Regular updates reflecting current regulations
- Performance Monitoring
- Skills gap analysis
- Compliance tracking dashboards
- Individual employee progress reports
These digital training tools ensure consistent knowledge transfer across teams while maintaining detailed records for audit purposes. The automated tracking system alerts managers when staff require additional training or certification renewals, creating a proactive approach to workforce development and safety compliance.
8. Audit Management
Digital audit management revolutionises the traditional inspection process through automated tools and real-time tracking capabilities. Modern food safety management software transforms complex audit procedures into streamlined digital workflows.
Key Digital Audit Features:
- Pre-configured inspection templates
- Digital checklists with automated scoring
- Photo documentation capabilities
- Non-compliance flagging systems
- Corrective action tracking
The software’s real-time reporting capabilities enable immediate identification of non-compliance issues. When violations occur, the system triggers automated alerts to relevant stakeholders, allowing swift implementation of corrective measures.
Digital audit trails create permanent, tamper-proof records that demonstrate compliance history. These records prove invaluable during external audits and regulatory inspections, providing instant access to:
- Historical compliance data
- Completed inspection reports
- Corrective action documentation
- Verification of resolved issues
The automation of audit processes reduces human error, ensures consistent evaluation standards, and creates a standardised approach to food safety inspections across multiple locations.
9. User-Friendly Interface
A user-friendly interface is a critical factor in the adoption of food safety management software. An intuitive design reduces resistance to change and speeds up implementation across teams with varying technical abilities.
Key attributes of accessible software design include:
- Clear navigation paths
- Logical menu structures
- Visual cues and icons
- Consistent layout patterns
- Mobile responsiveness
The ease of use directly impacts daily operations, allowing staff to:
- Complete tasks without extensive technical knowledge
- Access essential functions with minimal clicks
- Record data accurately in real-time
- Switch between different modules seamlessly
Software with minimal training requirements enables teams to:
- Start using core features immediately
- Master advanced functions progressively
- Adapt to updates without disruption
- Focus on food safety tasks rather than software mechanics
A well-designed interface reduces human error, speeds up task completion, and increases staff confidence in using the system. This enhanced usability leads to higher adoption rates and better compliance with food safety protocols at all operational levels.
10. Integration Capabilities
Modern food safety management software must seamlessly connect with various hardware devices and existing business systems. IoT integration capabilities enable real-time data collection from temperature monitoring sensors, humidity detectors, and other critical measurement devices across storage and preparation areas.
Essential Integration Features:
- Direct connectivity with temperature monitoring systems
- Automated data capture from IoT sensors
- Real-time alerts for temperature breaches
- Compatibility with food label printers
- Integration with freight monitoring systems
The software’s ability to integrate with enterprise resource planning (ERP) systems creates a unified operational environment. This integration enables:
- Centralised data management
- Automated inventory tracking
- Streamlined supplier communications
- Consolidated reporting capabilities
- Real-time visibility across operations
Advanced APIs allow the software to connect with:
- Quality management systems
- Supply chain management platforms
- Customer relationship management tools
- Financial management software
- Document management systems
These integration capabilities eliminate data silos, reduce manual entry errors, and provide comprehensive operational oversight through a single platform.
Additional Benefits of Food Safety Management Software
Food safety management software delivers substantial advantages beyond basic compliance and safety protocols. These systems create a ripple effect of improvements across operations:
Enhanced Supply Chain Communication
- Real-time data sharing between suppliers, manufacturers, and distributors
- Instant alerts for quality issues or delays
- Centralised platform for stakeholder collaboration
- Streamlined documentation exchange
Brand Protection Through Risk Mitigation
- Early detection of potential safety breaches
- Rapid response capabilities for quality concerns
- Digital audit trails for accountability
- Consistent quality maintenance across locations
Financial Advantages
- Reduced food waste through better inventory management
- Decreased likelihood of costly product recalls
- Lower insurance premiums due to improved risk management
- Optimised resource allocation
The implementation of comprehensive food safety software transforms operational efficiency through:
- Productivity Increase: Automated processes reduce manual tasks by up to 60%
- Transparency Enhancement: Complete visibility into food safety procedures
- Cost Savings: Minimised waste and improved resource utilisation
- Data-Driven Decision Making: Analytics-powered insights for strategic planning
These systems enable organisations to maintain high safety standards while achieving operational excellence. The digital transformation of food safety processes creates a competitive advantage through improved accuracy, efficiency, and reliability.
Implementation Considerations When Choosing Software
Selecting the right food safety management software demands careful planning and strategic evaluation. A comprehensive business needs assessment serves as the foundation for successful implementation.
Essential Pre-Implementation Steps:
- Conduct a thorough audit of existing processes
- Document specific compliance requirements
- Identify integration needs with current systems
- Set clear implementation timelines
- Establish success metrics
The deployment strategy must align with operational workflows to minimise disruption. Creating a phased rollout plan allows for systematic testing and adjustment of the system across different departments.
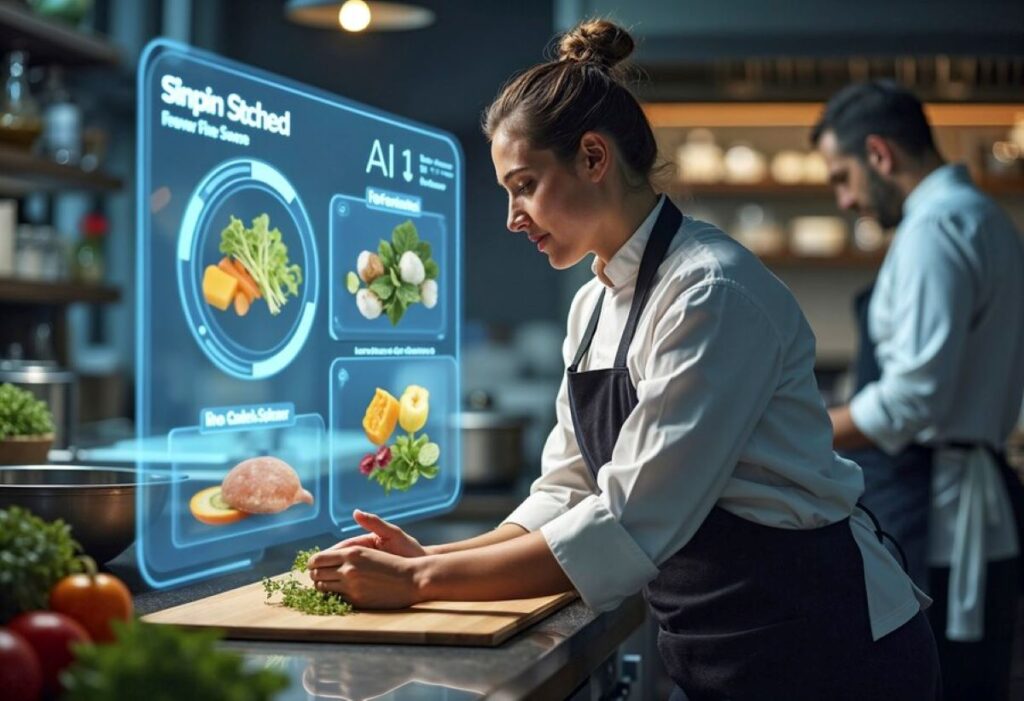
Team Training Requirements:
- Customised training programmes for different user roles
- Hands-on practice sessions with the new system
- Regular feedback collection from end-users
- Documentation of standard operating procedures
Vendor Evaluation Criteria:
- Track record in the food safety industry
- Client testimonials and case studies
- Technical support availability
- System uptime guarantees
- Regular software updates and maintenance
- 24/7 customer support channels
A reliable vendor demonstrates commitment through responsive support channels, including live chat, phone, and email assistance. The vendor’s expertise in food safety regulations and industry best practices strengthens the implementation process.
The software’s scalability must accommodate future business growth and changing regulatory requirements. Regular system audits and performance reviews ensure the solution continues to meet organisational needs.
Case Study Highlight – Squizify as a Comprehensive Solution
Squizify is a great example of modern food safety management software, providing strong solutions across various industries. This cloud-based SaaS platform shows how important features are used in real-life situations.
Key Implementation Success Points:
1. Automated Record-Keeping Excellence
- Digital temperature monitoring across 200+ locations
- Real-time compliance tracking
- Paperless documentation system
2. Customisation Capabilities
- Tailor-made checklists for specific industry requirements
- Adaptable workflows for different operational needs
- Scalable solutions for businesses of varying sizes
The platform’s success comes from its practical use in different sectors:
“Squizify has transformed our multi-site operations, reducing compliance monitoring time by 75% through automated systems and centralised reporting” – Leading Healthcare Facility Manager
Industry-Specific Solutions:
- Healthcare facilities: Temperature monitoring for medical storage
- Hospitality: Food safety compliance tracking
- Manufacturing: Supply chain documentation
- Aged care: Dietary requirement management
- Childcare centres: Allergen monitoring
- Retail: Stock rotation tracking
The platform’s 24/7 accessibility ensures continuous monitoring and immediate response capabilities, helping businesses maintain consistent food safety standards while reducing operational complexities.
Conclusion
Choosing the right food safety management software is a crucial decision for modern food businesses. The best solution combines strong HACCP planning, compliance tracking, automated workflows, and comprehensive supplier management capabilities. These essential features work together to create a secure and efficient food safety system.
Advanced software solutions like Squizify make it easier to manage food safety by turning a difficult task into a smooth process. When selecting software, it’s important to take a strategic approach by prioritising user-friendly interfaces, integration capabilities, and reliable support services. This will help businesses meet current food safety requirements and prepare for future challenges.
Investing in proper food safety management software brings long-term benefits such as improved operational efficiency, strengthened compliance, and protection of brand reputation.
More to Read : Benefits of Food Safety Inspection Software for Small Food Businesses